New sensor enhances efficiency and cybersecurity of critical facility operations
Platform developed at Los Alamos National Laboratory gives a holistic view of machines to ensure they’re working as they should
March 13, 2025
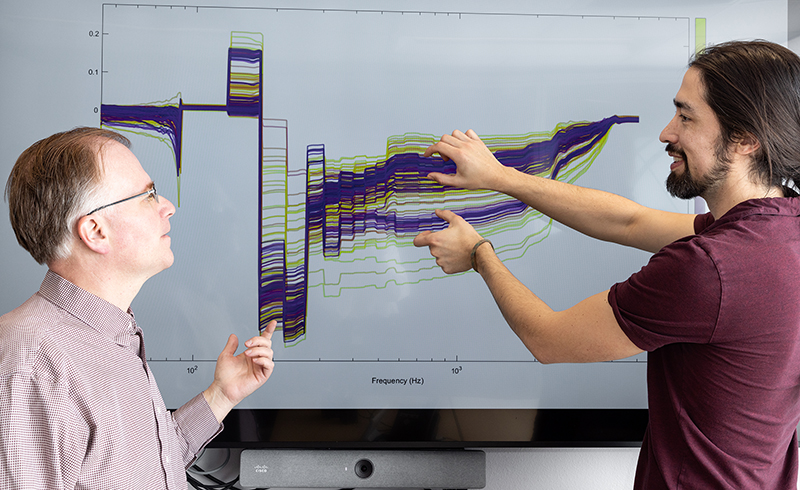
A new vibration-sensor technology, developed by a team at Los Alamos National Laboratory and enabled by artificial intelligence, improves the efficiency of plant and facility operations while enhancing cybersecurity to cost effectively monitor the flow of fluids through machinery.
Called Vibration Intelligence System for Industrial Operations and Networks, or VISION, the technology “enables a holistic view of an entire plant — like refineries or utility networks — to track total performance,” said Neil Loychik, the Los Alamos National Laboratory engineer who developed the technology. “It’s designed to overcome the limitations of traditional flow sensing by being low-cost and act as a layered cybersecurity measure by being independent of any control system.”
The platform — which will include a vibration sensor, signal conditioning, processor, wireless communication and a battery to install on a machine — uses artificial intelligence to monitor process parameters such as flow and pressure from the vibration.
To the average person, this might not seem important. But simple machines such as the pump, compressor and fan are the workhorses of modern society. They can be found in our heating and cooling systems, our refrigerators, and in more complicated systems such as water and sewage facilities, pharmaceutical manufacturing, power generation, oil and gas extraction, and mining. In fact, these simple machines account for nearly one-third of all electricity consumption.
“Fundamentally, these machines are designed to convert electrical power into mechanical power, which in turn drive the size and geometry of internal components,” Loychik said. “Pushing too much or too little flow through these geometries causes hydrodynamic and other potentially damaging forces, which can then lead to the premature failure of the machine.”
He adds that operating in this manner is inefficient because the power from the motor is powering the useless hydrodynamic effects rather than making useful flow. In fact, multiple industrial and utility surveys suggest that upward of 9% of electric grid consumption goes toward useless, and therefore recoverable, work in pumps and compressors.
To stop this waste, continuous monitoring of the machine’s fluid properties with pressure gauges or flowmeters is required. However, the cost of the sensors, installation and wiring to accomplish this is prohibitive.
Consequently, controlling production is often achieved by manual or automated “throttling” of a valve to get the flow operators want. The problem with this is that machines can operate outside of their design ratings — too much or too little flow — and cause damage to themselves, which can result in leaks, fires or operational shutdowns.
Furthermore, long-term poor operation can cause excessive costs associated with maintenance, electricity and unplanned downtime.
Worse still is that these problems can be nefariously induced by a cyberattack. VISION operates completely independent from the control system, which enables it to verify the machine’s output against the control set point. Thus, a cyberattack against a machine with VISION would alert plant operators to the possible attack and initiate an investigation as well as heightened security measures to prevent damage to the facility or injury to personnel.
“At a fundamental level, the need for this technology is to verify that machinery is operating as intended, and to do so cost effectively in comparison to more expensive traditional sensors or motor controls,” Loychik said.
A patent is currently pending for this technology.
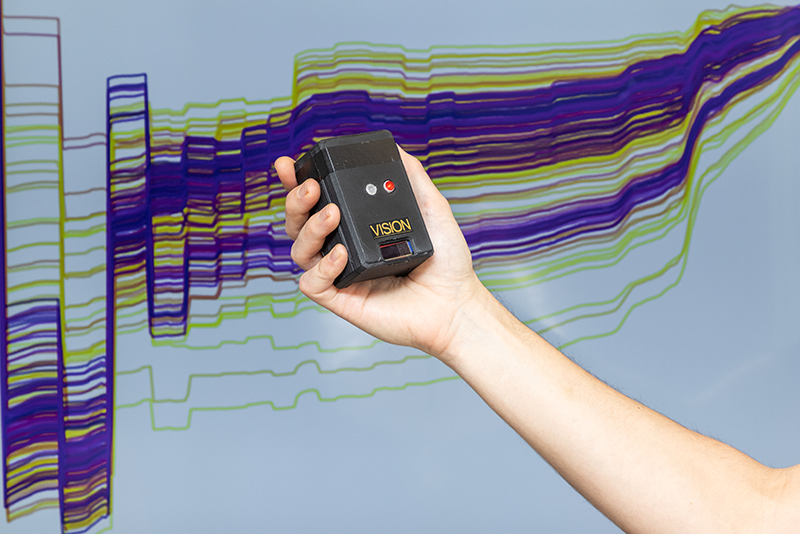
LA-UR-25-22375
Contact
Public Affairs | media_relations@lanl.gov