VISION: Vibration Intelligence System for Industrial Operation and Networks
Enhanced Industrial Efficiency and Security with Advanced Vibration Analysis
technology Snapshot
Overview
Over the lifetime of operating an industrial machine, plant managers will typically spend many times the purchase price of the machine on other activities like maintenance, electricity, and downtime for when the machine breaks. It is an ever-constant challenge and often a difficult choice to make equipment run smoothly (and thus reduce lifetime costs for operating the machine), or to meet short-term production targets. The consequence is that machinery is regularly pushed beyond its operational limits that cause failures, downtime, chemical release and fires. Worst, operating limits can be purposefully be exceeded in the event of an industrial cyberattack.
VISION solves this problem by using vibration to measure machine operating conditions, where plant managers can use this data to optimize costs-of-production, and detect cyber threats—without requiring integration into existing control systems. Built on advanced signal processing mathematics, VISION enables high-accuracy machine learning predictions with minimal computational overhead. Scalable and independent, it provides a holistic view of facility performance, helping industries like oil & gas, power generation, and chemical processing to reduce costs, prevent downtime, and enhance security.
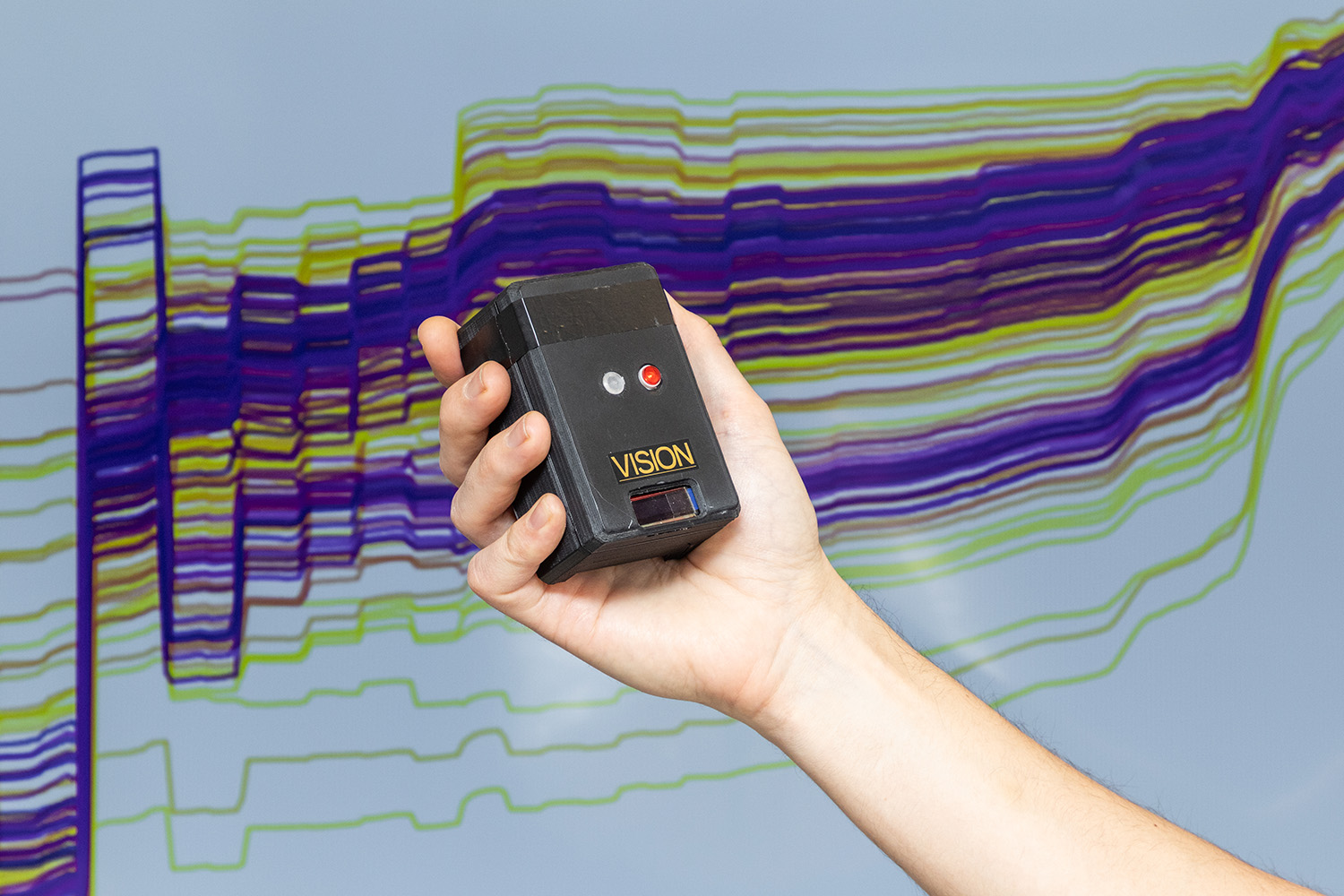
Advantages
- Comprehensive Facility Monitoring: Provides a holistic view of all machinery used in manufacturing, not just critical machines. Plant managers can better manage ‘forgotten’ machines that are manually controlled and not instrumented.
- Independent Cybersecurity Check: Monitoring is independent from an industrial control systems, providing a means to check for cyberattacks on the machine.
- Maximizing Insights with Minimal Hardware: Extracts valuable operational data using vibration sensors, reducing reliance on costly infrastructure upgrades for the same knowledge.
- Superior Machine Learning Performance: Uses higher-order spectral densities (HOSD) to improve AI-based predictions, reducing training time and increasing accuracy.
- Scalable & Non-Intrusive: Provides insights across the plant without modifying existing infrastructure, making it easy to implement and expand.
Technology Description
VISION leverages higher-order spectral densities (HOSD) to extract richer insights from vibration data than traditional power spectral density (PSD) methods. By capturing statistical characteristics such as skewness and kurtosis in the frequency domain, which are physical indicators of how a machine is running.
VISION enables:
- Operations Monitoring: Accurately monitors machine fluid characteristics (pressure / flow), which corresponds to a measure of efficiency, reliability, and failure mode.
- Cyberattack Detection: Identifies operation anomalies indicative of system compromise, independent of the control system and does not use internet monitoring like modern security solutions.
- Edge AI Processing: Performs on-device analysis with minimal computational burden, enabling faster and more accurate diagnostics.
- Integration with Condition Monitoring: Vibration data can be supplied to maintenance staff to detect equipment failure.
Market Applications
VISION serves industries where operational efficiency, predictive maintenance, and cybersecurity are critical. Examples of possible applications are:
- Oil & Gas: Extraction, pipelines, and refinery pumps and compressors, monitoring for poor operations that cause leaks and fires.
- Power Generation: Monitors cooling systems for optimal performance and safety.
- Chemical & Pharmaceutical Manufacturing: Ensures precise fluid control in sensitive production environments.
- Water & Wastewater Treatment: Maximize efficiency and reduce energy consumption from the facility to the city scale.
- Industrial Cybersecurity: Provides a cyber-physical security check against stealthy cyber threats like Stuxnet-style attacks.
Next Steps
VISION has demonstrated feasibility within a working prototype (TRL 5). The next phase requires investments to develop a custom sensor platform, including hardware design, sensors, processors, batteries, and wireless communications, as well as hazardous location (HazLoc) certification to operate in target industries.
Partner with manufacturers to:
- integrate VISION into existing industrial monitoring systems;
- conduct further validation trials to refine accuracy and scalability; and
- initiate product development and market deployment.