Researchers at Los Alamos National Laboratory advance cutting-edge manufacturing techniques to support national security.
December 9, 2024
Jake BartmanLook around, and you’re almost certain to find yourself within arm’s reach of a manufactured product. From carpeting to cardboard, computers to cars, the modern world consists largely of raw materials—metal ore, plant matter, petroleum, or any of countless others—that have been converted, by a series of industrial processes, into finished products.
Although the techniques used in manufacturing are innumerable, many key techniques were developed hundreds or even thousands of years ago. Take forging, for example. Forging—which involves shaping metal through a series of blows—has been in use since at least 4,000 BCE, when the technique was developed to make jewelry, tools, weapons, and other objects.
Forging looks far different today than it did in ancient Mesopotamia (hydraulic presses and computer-controlled tools have long since replaced stone hammers). But at its most basic, the technique remains the same: a piece of metal is repeatedly struck until the metal assumes a desired shape.
Over the past few decades, new techniques have redefined manufacturing as we know it. One major advance is the development of additive manufacturing (also called 3D printing) in the 1980s. Unlike traditional techniques that can involve cutting, machining, stamping, or otherwise removing pieces from a raw material until the material assumes a desired shape, additive manufacturing involves applying layers of material, one on top of another, to create a structure.
3D printing isn’t the only technique that is changing the way society thinks about manufacturing. Advances in sensing technology have made it possible to monitor manufacturing processes in real time. Developments in computing have led to sophisticated modeling programs that can take into account the unique properties of diverse materials. And innovations in the field of robotics are allowing for the automation of all kinds of tasks that are repetitive or potentially dangerous.
Taken together, these methodologies are sometimes described as “advanced manufacturing”—a catchall term that encompasses both new approaches to manufacturing and the ways in which innovative methods can augment older ones.
At Los Alamos National Laboratory, researchers are developing and exploring novel advanced manufacturing methods. In doing so, researchers are supporting the nation’s nuclear security enterprise at a time when the enterprise is manufacturing key weapon components on a scale not seen since before the end of the Cold War.
“To have a responsive enterprise, we must revolutionize manufacturing technology,” says John Bernardin, a researcher in the Laboratory’s Modern Manufacturing Methodologies group. “At Los Alamos, we have the ability to rapidly perform manufacturing research and enable the down-selection of technologies for the production of weapon-related components.”
In January 2024, the Laboratory identified advanced manufacturing as one of five signature institutional commitments that must be pursued to help Los Alamos achieve its national security mission. The goal, according to the Laboratory Agenda—an annual comprehensive framework that aligns Los Alamos’ long-term objectives with concrete, near-term milestones—is to ensure the Laboratory’s ability to rapidly develop prototypes. In this way, the Laboratory will “build, qualify, and certify new components with new manufacturing technologies” that could be adopted for use throughout the nuclear security enterprise.
Across Los Alamos, researchers are developing new manufacturing methods and technologies that support the Laboratory Agenda’s mandate. Researchers in materials, computer codes, 3D printing, and other areas are helping the Laboratory to achieve diverse manufacturing-related goals. Bernardin helps lead an additive manufacturing working group that aims to coordinate Los Alamos’ research and development (R&D) efforts related to advanced manufacturing. The Laboratory, Bernardin says, is the right place to conduct research into cutting-edge manufacturing technologies that will support the nation’s security.
“Our expertise in manufacturing science and R&D has always been connected to our knowledge of weapons physics, weapons engineering, and computational modeling. It all works together,” Bernardin says. “We know our weapons better than anybody else.”
3D printing ceramics
Additive manufacturing is one area in which Los Alamos conducts significant research. The Laboratory acquired its first 3D-printing capabilities in the 1990s. Over the years, as additive manufacturing technologies have advanced, Los Alamos’ exploration of the technology has evolved apace.
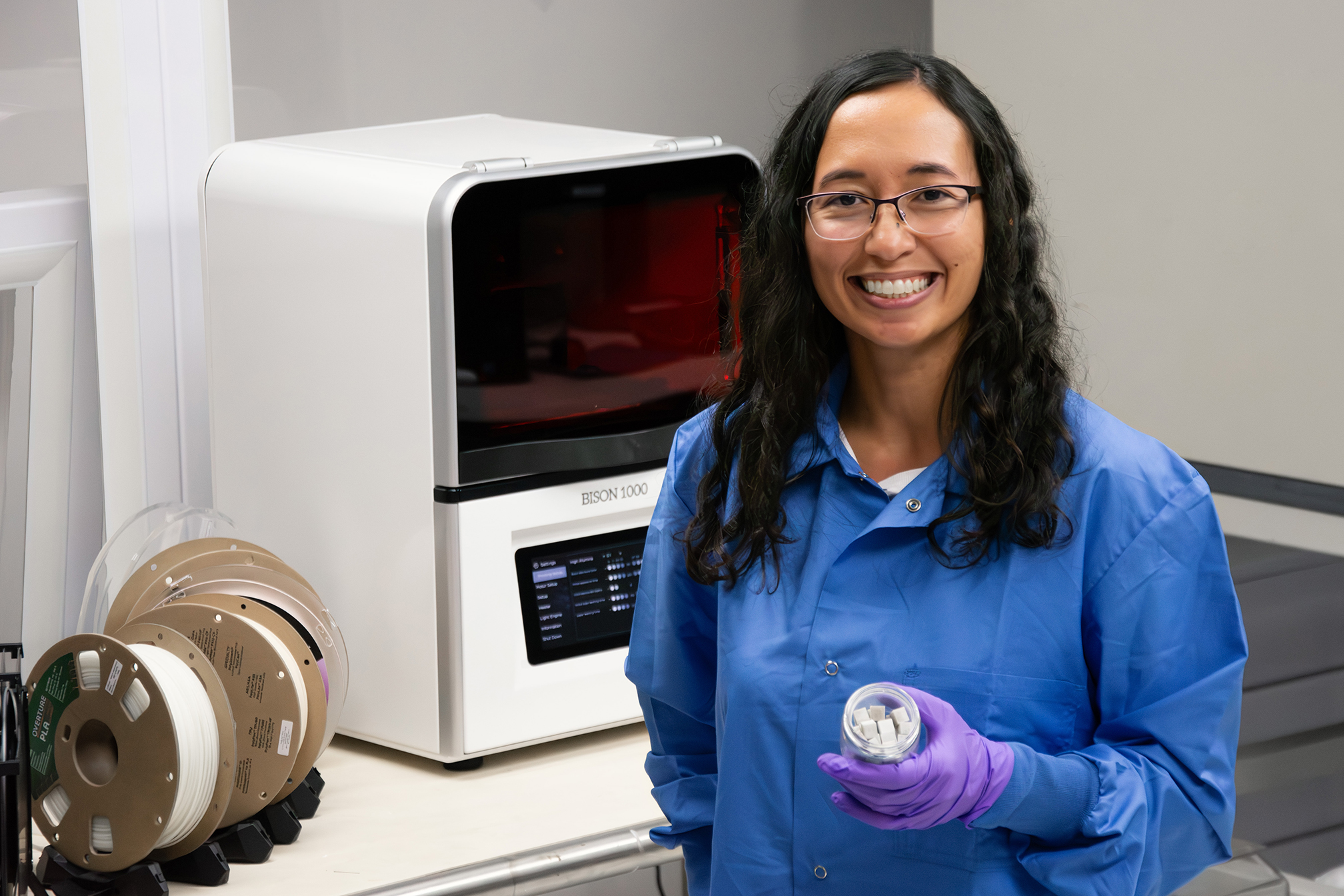
“You hear people say, ‘3D printing is going to revolutionize the world,’” says Lindsey Bezek, a postdoctoral researcher in the Laboratory's Chemical Diagnostics and Engineering group. “While I can’t say what the future will bring, what I can say with certainty is that 3D printing offers a unique—and thus sustainable—alternative manufacturing solution with many promising directions.”
Today, the Laboratory conducts research into many kinds of 3D-printing technologies. Los Alamos’ size and diversity are such that you’ll find researchers exploring virtually every aspect of the additive manufacturing process, including the materials that are used as feedstock (the polymer, metal, or other material that is fed into the machine and deposited to make an object), the tools that deposit material, the software that guides those tools, the post-production processes required to “finish” additively manufactured parts and certify their quality, and more.
“A promising direction in additive manufacturing is the integration of the materials, the process, and the design,” Bezek says. “At the Laboratory, we have so many different groups that can approach the subject from different angles.”
Bezek’s work reflects the way that researchers at Los Alamos bring varied perspectives to bear on additive manufacturing research and development. Although she earned her PhD in mechanical engineering, for the past two years, Bezek has been a part of the Laboratory’s Chemistry division, where she researches the properties of materials used in 3D-printing technologies. Among other subject areas, as a part of her postdoctoral fellowship, Bezek is conducting research into 3D printing ceramics.
For most people, the term “ceramics” brings to mind porcelain or earthenware pottery. Technically, a ceramic is a nonorganic, nonmetallic material—such as clay or silica—that has been shaped and heated to a high temperature. Today, high-end ceramics are made not with clay but with elemental oxides that yield ceramics with specialized properties. Researchers at Los Alamos have worked with ceramics for decades, developing them for use in everything from satellites to nuclear reactors.
Although ceramic 3D printing has a breadth of applications—from making electronic and aerospace components to dental crowns and joint replacements—ceramic 3D printing is a much smaller part of the commercial industry than metal or polymer additive manufacturing. (Polymers are long chains of molecules with repeated units, like plastics.)
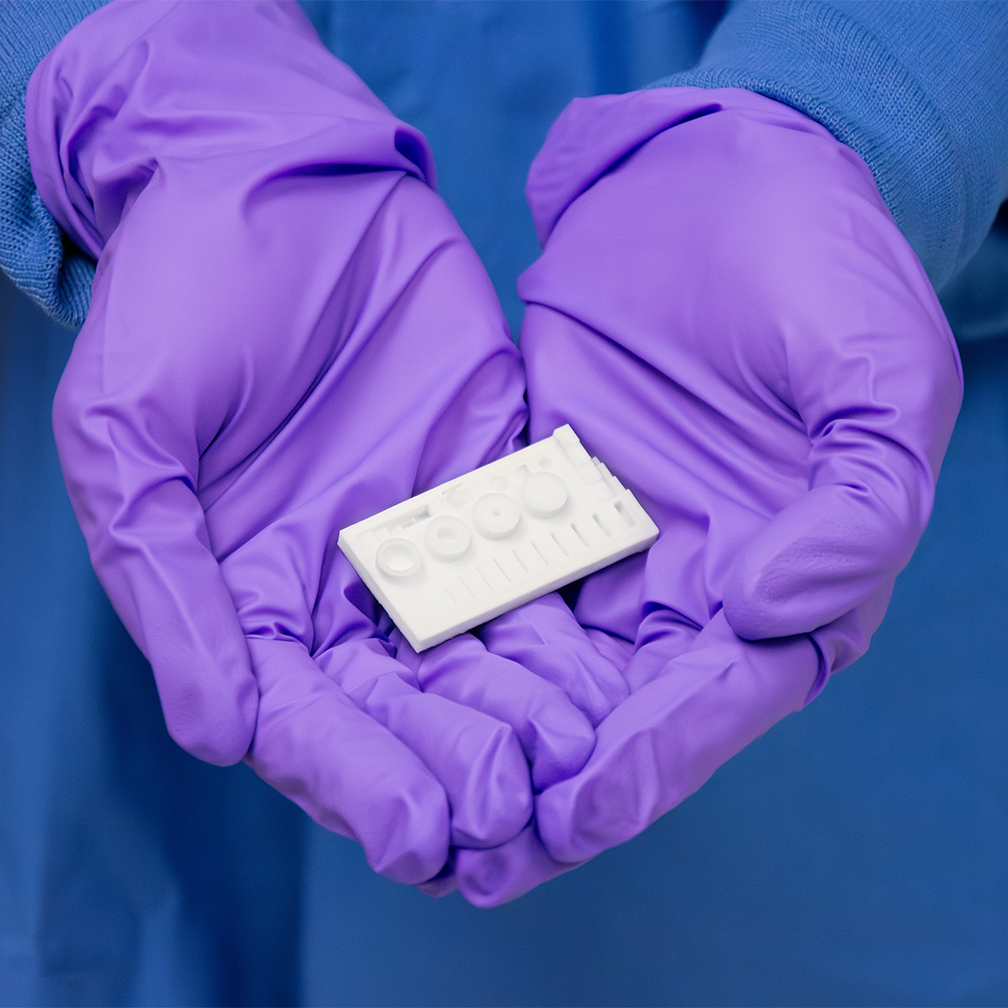
Bezek says that there is a need for additional research into ceramic 3D printing to increase quality assurance before industries can confidently invest in the technology. At the Laboratory, Bezek works to understand some of the fundamental processes that take place when ceramics are 3D printed and processed.
One of the most common techniques for 3D printing ceramics is called vat photopolymerization. This technique involves using a beam of ultraviolet light to harden layers of liquid resin—a mix of polymer and ceramic particles—one on top of another to produce a part.
Other kinds of 3D printing (with metal or polymers, say) can result in parts that are finished as soon as they’ve been printed. Ceramic 3D printing is different: After a ceramic part is printed, it must be heated before it’s ready for use, much as clay pottery must be fired in a kiln. This heating process “burns out” the polymer particles that previously held the ceramic molecules together and fuses the ceramic particles into a hardened, sintered part.
Vat photopolymerization is a well-researched technique; in fact, it was one of the first 3D-printing techniques developed. However, the heating process that’s necessary to finish a 3D-printed ceramic part is less well researched. Sometimes, the heating process can result in parts that are cracked or otherwise defective.
The causes of such failures remain poorly understood by additive manufacturing researchers. Bezek’s research involves attempting to understand exactly what causes these undesirable results. By heating ceramic parts of a variety of shapes and sizes, and by tracking the parts’ characteristics when exposed to different amounts of heat for different lengths of time, Bezek is able to better explain how temperature and time affect 3D-printed ceramic parts at very small scales.
“The benefit here is learning how to design for ceramic additive manufacturing,” Bezek says. “We’re working toward predictable part performance for future design and manufacture of complex, functional parts, and we’re moving toward using novel materials in the future.”
Multi-axis 3D printing
Although 3D printing allows for the rapid creation of complex parts, the technique has limits. For one thing, most 3D-printing technologies can only create parts out of a single feedstock.
For another, 3D-printing tools struggle to make certain shapes. Because 3D-printed parts are manufactured layer by layer, gravity can be a limiting factor. In the same way that it is more challenging to build a brick wall on a steep slope (the bricks are likely to slide out of place) than on level ground, it can be difficult to ensure that layers of material applied additively will stay put on slanted or uneven surfaces. This drawback requires designers to incorporate cumbersome support structures into objects.
A new multi-axis 3D printer that’s being evaluated by the Laboratory’s Modern Manufacturing Methodologies group could help overcome both the material constraints and the challenges posed by gravity. The 3D printer, which was designed by One-Off Robotics, uses fused deposition modeling (FDM)—one of the most common 3D-printing techniques—to melt polymer filaments into a desired shape.
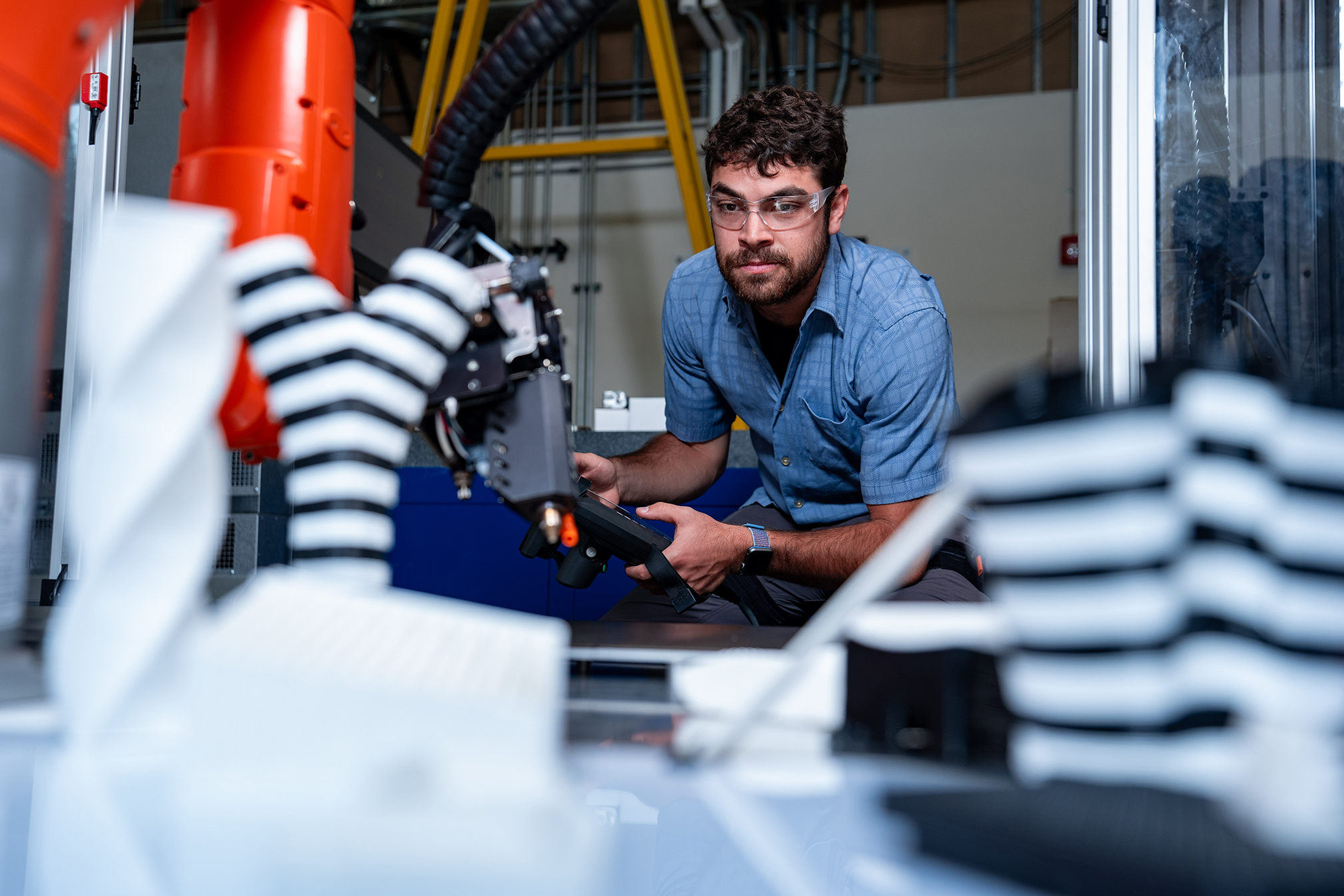
Traditional FDM 3D printers use a gantry (a bridge-like structure from which the 3D printer–head is suspended) to move their tool heads either horizontally or vertically. In recent years, however, researchers have found that using a robotic arm, which has a much greater range of motion, allows them to print different kinds of shapes.
“Robotic arms have been around for decades, and they haven’t really changed much,” says Andre Bos, a researcher who studies multi-axis 3D printing. “But the software has developed a lot, which has made it possible to apply material along nonplanar paths.”
The ability to apply material in nonplanar, or non-horizontal, ways makes it possible to 3D print structures that are thinner or more complex than can be created with traditional additive manufacturing techniques. Moreover, the ability to 3D print in this way means that some complex parts can be printed without cumbersome features designed to support the structure. This technique also allows material printing onto existing structures, making it possible to repair damaged or worn components.
Bos and other researchers have printed a variety of test objects, the better to understand the limits of this new technology and how it might be further developed in support of the Laboratory’s mission.
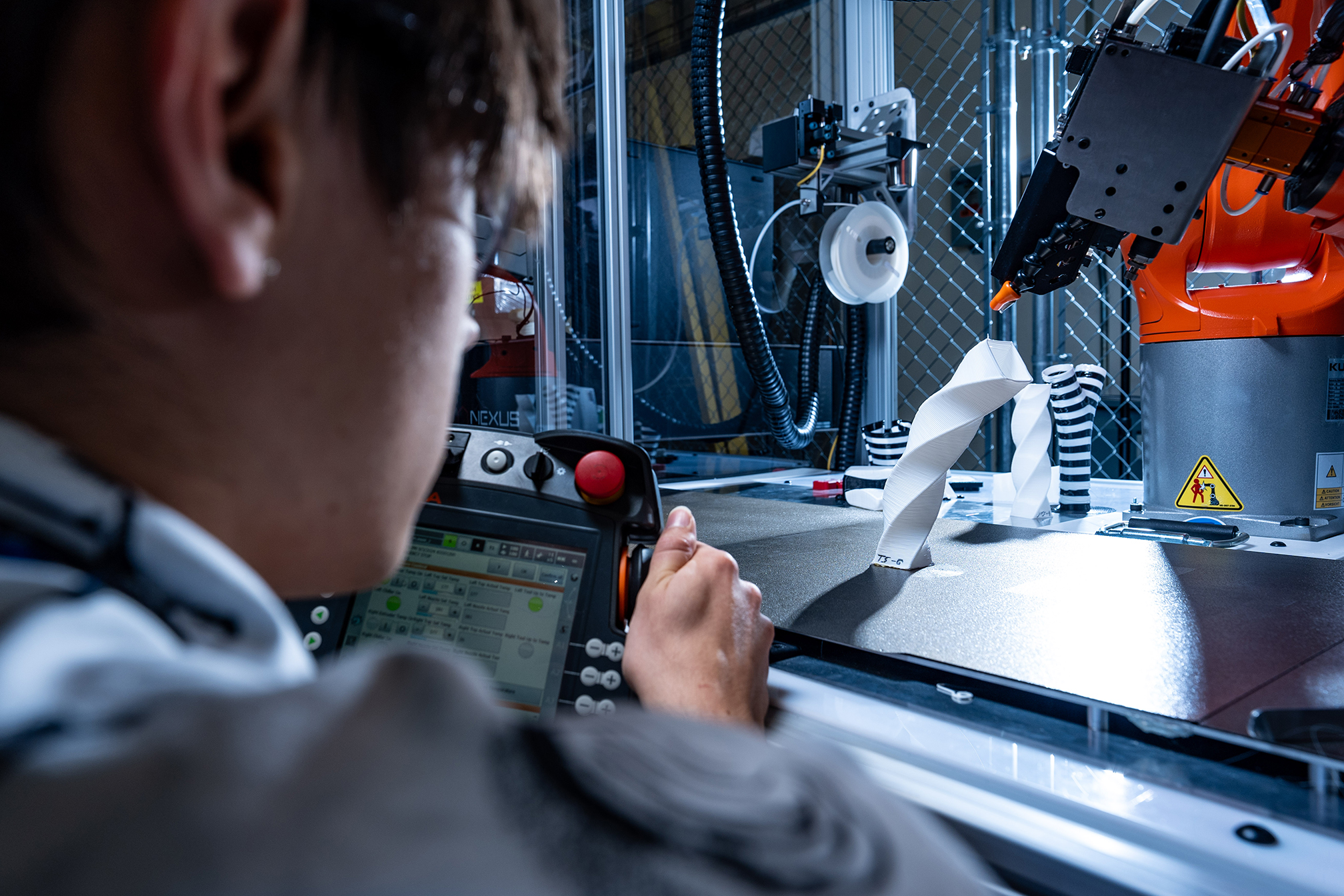
Combining robotics with 3D printing opens other doors as well. The multi-axis system that Bos is helping evaluate also has the capacity to change its printer heads automatically. That capability allows the robot to print objects made of more than one material. The robot can apply a few layers of one material, change printer heads, apply a layer of another material, change heads again, and so on.
In principle, multiple robotically controlled 3D printers could also be coordinated to work together to print ever more complex structures. “What robotics really means is that if we spend the time to develop the control mechanisms and to integrate the software and hardware, we can print basically whatever we want,” Bos says.
Process monitoring
In industry, manufacturers often take some waste for granted: It is understood that a certain percentage of finished parts will fail to meet specifications and be thrown away. At Los Alamos, however, machinists often work with extremely valuable metals that can’t be discarded as readily as, say, an aluminum aircraft component.
To better ensure that such metals don’t go to waste, Laboratory researchers are working to develop techniques that will allow machinists to ensure that the parts they’re creating are on track to meet specifications.
One way to help ensure accuracy is by incorporating a laser scanner into the manufacturing process. A machinist working with a lathe might make three or four “passes” over a piece of metal, working with each pass to bring the metal nearer to a desired shape. By pausing after one of these passes and using a laser scanner to take several “pictures” of the surface of the part, a machinist can see, in high resolution, how the part’s creation is progressing.
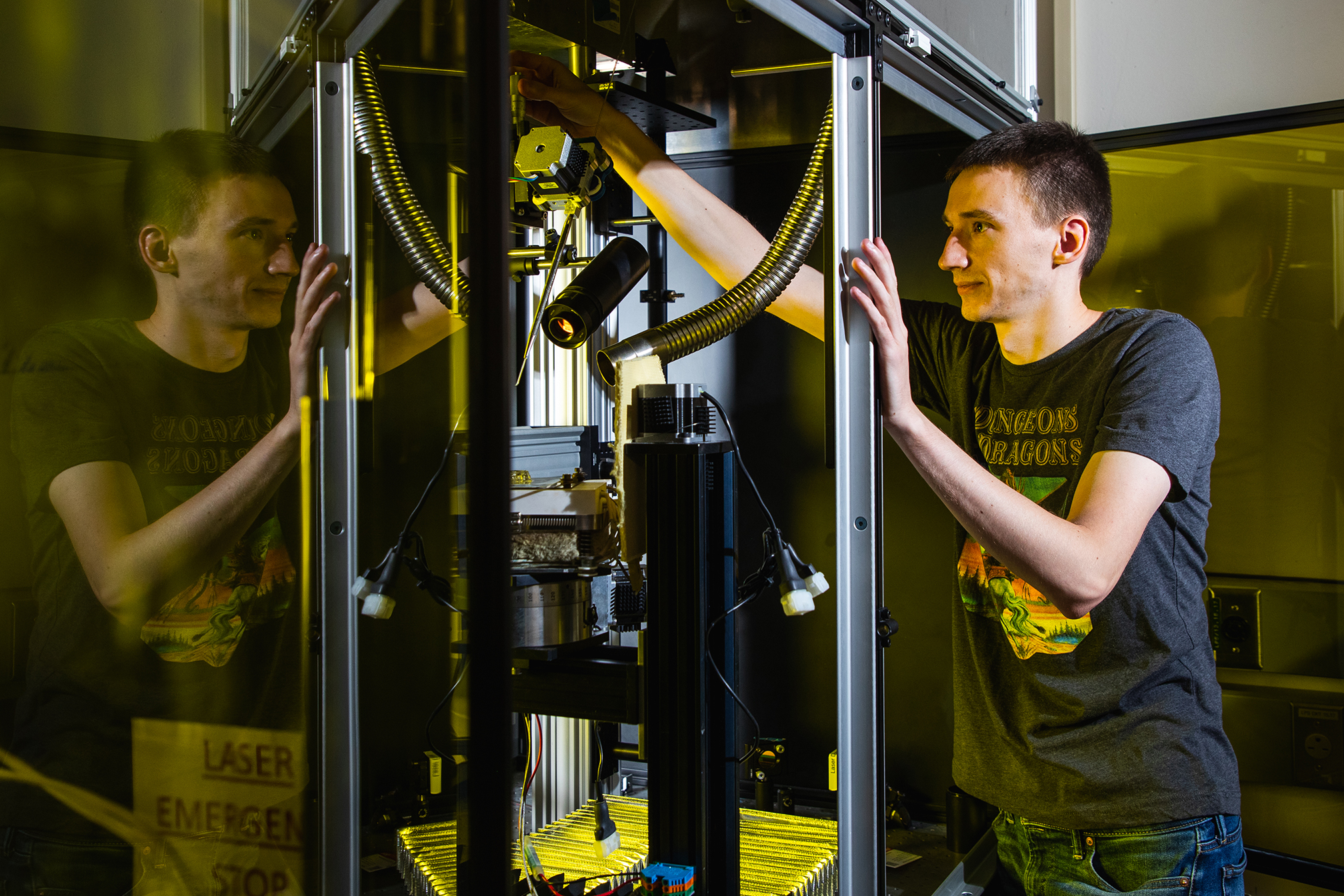
This technique has several advantages. For one thing, the procedure takes only a few seconds to complete. For another, it is comprehensive, allowing an operator to inspect the entirety of a part with relative ease. And because the scan is optical—the scanner doesn’t have to physically touch a part to inspect it—the measurements can’t be inadvertently altered.
Laser scanning does come with challenges. Many high-value parts manufactured at Los Alamos have curved geometries. Because laser scanning is an optical technique that relies on the reflection of light off a surface, laser scanners often struggle to accurately scan curved surfaces. However, researchers at the Laboratory found ways to overcome these difficulties, and Bos says that the technology is ready for deployment. He and other researchers are working to further develop the system, envisioning a day when robotics might make laser-scanning parts fully automated.
“By implementing this additional monitoring and inspection system, we’re making the process smart,” Bos says. “We’re providing machinists with tools that can make their manufacturing better.”
3D printing glass
Today, it is possible to 3D print many kinds of materials, including concrete, food, and high explosives. And yet, one of the materials that’s the most challenging to 3D print is an integral part of day-to-day life: glass.
Glass is challenging to print for several reasons that, taken together, necessitate the combined use of robotics and sophisticated monitoring techniques. Glass must be heated to a very high temperature to become soft enough to shape. However, overheating the glass can affect its optical quality: Once deposited, glass can appear cloudy or distorted because of bubbles or the vaporization of substances—defects that can be especially problematic if the glass is for applications like optical lenses.
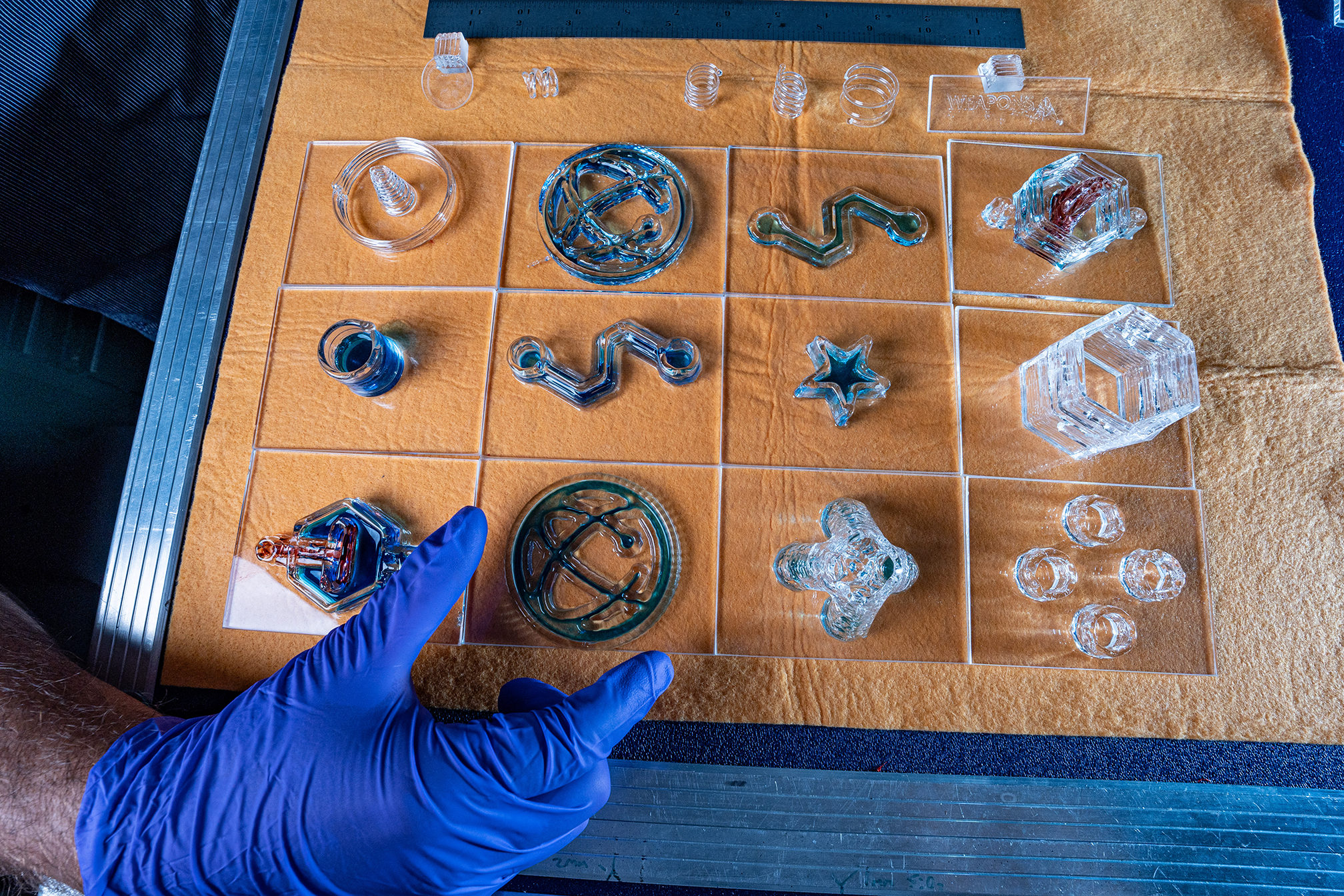
At Los Alamos, researchers have followed the lead of researchers at the University of Notre Dame in developing a system to 3D print glass. First, a laser melts a glass rod, which is about the width of a strand of spaghetti, onto a build plate (a rectangle of heated glass). Then, using a robotic system to move the build plate as the glass rod is melted, a 3D glass structure can be printed.
Precisely controlling the temperature of the glass is key. This constraint requires on-machine monitoring to observe the glass as it is melted. Bos and other researchers found that by focusing cameras (including thermal cameras), spectrometers, and pyrometers on the point where the laser melts the glass, it is possible to monitor the melting and adjust the laser’s temperature as needed.
Unfortunately, different glass types have varied chemical compositions, meaning each type requires different printing and temperature parameters. Determining these parameters is, at present, a tedious process of trial and error, although researchers are working to find ways to speed up this kind of analysis.
Another challenge has to do with the propensity of glass to crack under temperature-induced stress. In much the same way that a glass casserole dish can shatter if moved from an oven into a refrigerator, when a layer of hot glass is applied atop cooler, previously deposited layers of glass, the cooler glass is liable to crack. That means that to manufacture a glass structure any taller than an inch or so, it is necessary to keep the entire structure hot. Researchers at the Laboratory who have produced small test prints in a variety of shapes are seeking ways to address this need.
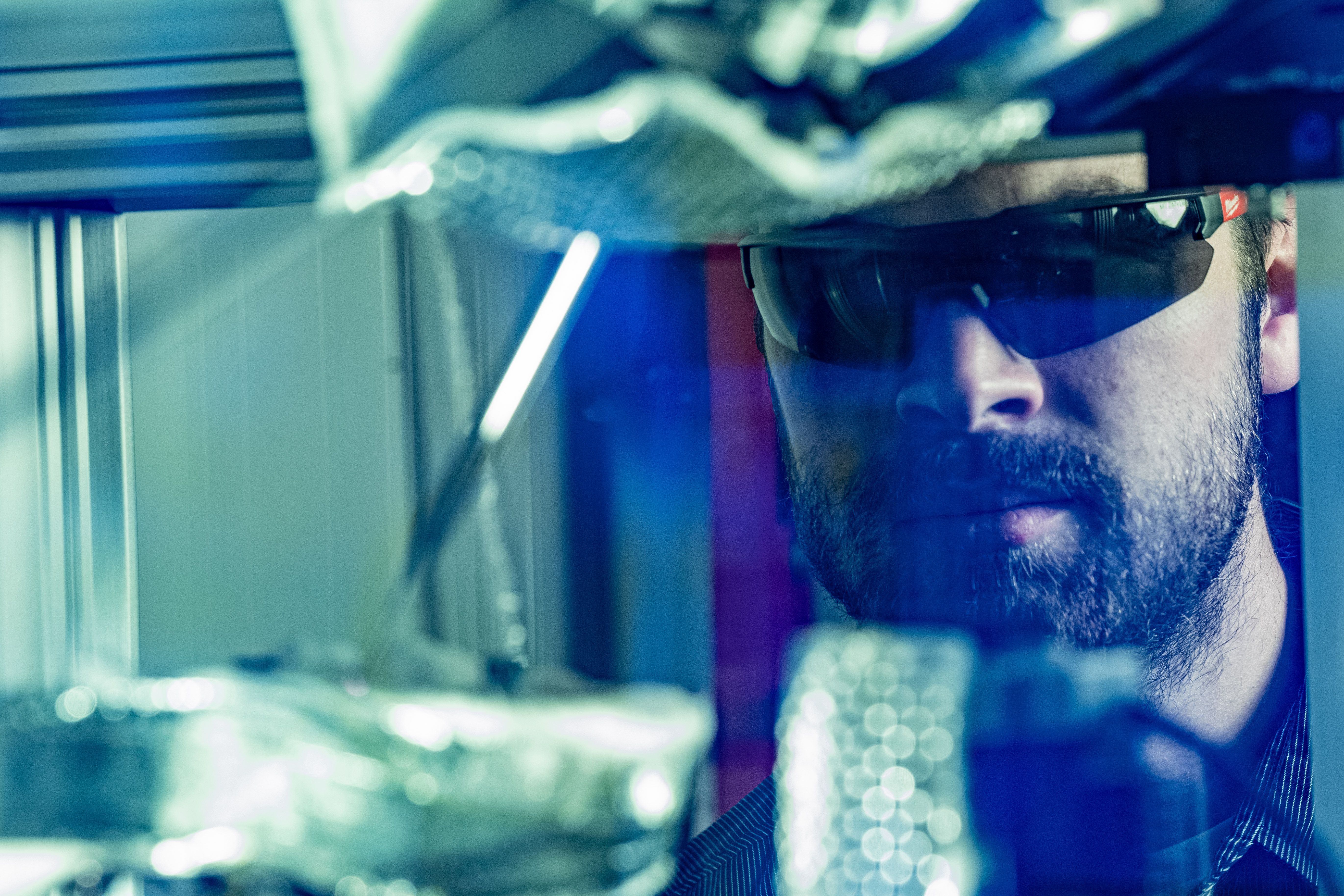
Beyond advancing the science of additive manufacturing, there are practical reasons to 3D print glass. Many laboratory experiments rely on complicated glassware that might ordinarily be manufactured by skilled glassblowers. However, glassblowers are in ever shorter supply, meaning that some important pieces of equipment are becoming more and more difficult to acquire. And even the most skilled glassblowers can’t produce glass in certain shapes.
“You can only do certain things with glass blowing, and you can only get so much accuracy,” Bos says. “If you want greater accuracy and complexity, or if you want a square shape rather than a round shape, glassblowers can’t do that very repeatably.”
Bos says that the capacity to 3D print glass will help ensure that the Laboratory has the resources it needs to continue to achieve its mission.
“One of the main reasons to use 3D printing is to make repeatable, complex structures,” Bos says. “We need to be able to find a way to make these structures for the future.”
Real-world applications
One of the ways that researchers put advanced manufacturing techniques to use is in developing new types of shielding for Laboratory employees who work with radioactive materials.
Researcher Nick Baumann is part of a team that’s creating new types of radiation shielding for workers in the Laboratory’s Plutonium Facility (PF-4) by developing gloves, panels, and windows for gloveboxes (specialized enclosures that workers use to contain hazardous materials). These new shielding technologies are intended to provide greater protection while eliminating the use of lead, which has traditionally been used throughout PF-4.
“Lead is hazardous, and its use produces mixed waste,” Baumann explains. “If you need to dispose of a leaded glovebox window or gloves, you might have something that is both radioactive and has lead in it. So, you have a compounded problem.”
The shielding materials team is developing shielding technologies that use tungsten metal rather than lead. This new type of shielding has other advantages, too. By manufacturing the shielding using advanced techniques, it is possible to create shielding that is lighter, stronger, and more effective.

The shielding materials team is evaluating three distinct processes within PF-4 and exploring avenues for replacing or augmenting the shielding involved in each. Already, the team has completed its evaluation of a pyrochemical process (which involves exposing materials to high temperatures), determining that with improved, additively manufactured shielding, it is possible to reduce workers’ yearly radiation exposure by 34 percent, helping ensure that these workers’ radiation exposure remains at safe levels.
In addition to benefiting workers’ health, reducing radiation exposure means that workers can perform more tasks before reaching exposure limits set by the Department of Energy and the Laboratory. That could increase the productivity of this pyrochemical process by 65 percent, Baumann says.
Much of the new shielding—including pieces that can be used inside a glovebox to control radiation exposure and wrist cuffs that can be worn to provide additional radiation protection—can be 3D printed. Researchers use a filament made of polylactic acid, or PLA (a polymer made from renewable sources), and tungsten to create custom shielding for use inside gloveboxes. By 3D printing tungsten PLA, it is easier to fabricate high-density parts than by traditional methods: Tungsten is extremely dense and abrasive, making the metal notoriously difficult to machine.
The shielding materials team is exploring related uses of 3D printing, too. For example, the team has demonstrated that it is possible to laser scan a worker’s arm, and to use that scan to 3D print a mold and design a custom glovebox glove for the worker. Gloves produced from molds in this way could also be designed to have different levels of shielding, depending on which part of the arm will receive the greatest radiation dose.
Baumann says that while some types of shielding, such as the gloves and glass, could be mass produced by commercial vendors after they’ve been developed, the ability to 3D print shielding blocks at the Laboratory means that new pieces of shielding can be produced on demand to help the Laboratory achieve its production mission.
“The configuration of the equipment inside the glovebox could change, but you want shielding that can be conformal and fit around things,” Baumann says. “Additive manufacturing is perfect for that.”
A manufacturing powerhouse
Although the techniques that Baumann and other researchers are developing at Los Alamos are novel, Bernardin says that their development comes from a tradition of manufacturing-related work that stretches back to the Laboratory’s earliest days. The goal, Bernardin says, isn’t to dispense with traditional manufacturing techniques. Instead, developing and implementing novel manufacturing techniques at Los Alamos will help the Laboratory—which he describes as “a manufacturing powerhouse”—to better achieve its mission.
“We’re working to get these new technologies to a place where we can use them reliably,” Bernardin says. “But we’ll still have the old technologies, too—and that’s what’s exciting.” ★